Understanding your sewing machine’s tension system is the single most important thing you need to know to become an incredible stitching queen (or king). However, tension is often the most confusing aspect of your machine and we aren’t taught much beyond turn it this way to loosen the top tension and that way to tighten it. So, most of us just leave that dial alone and never move it off of the little line in the middle that is supposed to give us perfect tension.Before I hand out my great tips for understanding your machine’s tension let’s get a few technical terms down.
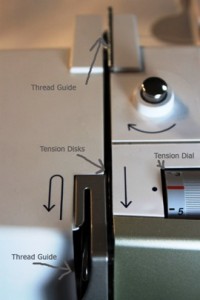
Balanced Tension: achieved when your upper and lower threads meet in the middle of your seam or quilt. The top thread is not visible on the underside and the bobbin thread is not visible on the top of whatever you are stitching.
Unbalanced Tension: tension is not balanced and either the top thread is visible on the underside or the bobbin thread is visible on the top. Unbalanced tension can be used for cool special effects.
Tension Dial: an adjustable dial (technically called a regulator) on your sewing machine that allows you to increase or reduce the tension on your thread. Some computerized machines have adjustments located on the programing board and you push a button to adjust the tension but we still call it the tension dial just because…well because we always have.
Tension Disks: two disks through which the thread passes when you thread your machine. These disks squeeze together to put tension on the thread. The amount of pressure put on the thread is determined by the setting on the tension dial.
Thread Guides: These are hooks or slots along the threading path for your machine. They add a little tension to the thread as they guide it in the proper direction to the needle. If you skip a thread guide you will reduce the thread tension a teensy amount.
If you always use the exact same thread in the top and bobbin, keep your machine clean, have it serviced often, change your needles regularly and always stitch with the feed teeth (dogs) up you may never have to adjust your upper thread tension. But, if you are stitching a little on the wild side and like to play with more than one type of thread, keep reading!
One of the first things I explain to my students is that there is no one right answer for which tension setting to use with a particular thread and fabric combination. The unique settings for each and every sewing machine vary. Humidity (or lack of) and temperature effect your thread, fabric and machine. Additionally, the age and health of each machine is as much a factor as the disposition of the machine operator is.
The very best exercise for understanding your machine’s upper tension settings with different thread combinations is one that I developed when I began teaching my Stitch Journeys classes. It doesn’t take much time and will give you a wealth of knowledge about your machine.
You will need the following supplies:
Fabric: choose a medium to light color solid or mottled fabric. Cut to 5″x7″ in my sample but you can make it larger if you like.
Thread: choose an assortment of specialty threads. This sample uses a Silk 100wt., a Rayon (medium wt.), Metallic, Cotton (medium wt.) and a Rayon (heavy wt.). Choose a contrasting color thread for the bobbin in a medium wt. cotton.
Tear away stabilizer
Fine tip marker
Use a Sharp or Microtex needle.
Change needles as needed for larger or metallic threads.
Assumption: Most machines have adjustments from 0-9 or 10. If yours has fewer or more simply adjust the number of grid lines you draw.
STEPS
1. Draw horizontal grid lines on your fabric 3/4″ apart or further apart if making a larger sample. I stitched my lines for extra stitch fun.
2. On the left side, write the numbers 0-8. These are the tension settings you will test. It is not necessary to go to a 9 or 10 tension setting because the fabric will usually begin drawing up and puckering because the tension is high. Set up your machine for a zigzag stitch (as wide as possible with a slightly shortened length-about a 1 to 1.5) and choose one of the specialty threads. Choose the needle down option if available
3. Begin at the top of the grid with the upper tension disks set to ‘0’. Stitch to the first grid line.
4. With the needle in the down position, lift the presser foot, adjust the tension dial to next high number. Lower the presser foot and stitch to the next grid line. Repeat all the way down the length of your fabric changing tension at each line. Always lift the presser foot to change your tension setting or it will take a few stitches to register the change.
5. Repeat the process with different threads in vertical rows across the width of the fabric. Write the thread fiber and weight next to each sample.
What You Get!
You now have a visual record of the settings that work best for each thread you use. This may not be a guarantee across different brands but it gives you a starting point. Look at the metallic thread stitching in the middle column of my sample. I had a lightweight poly thread in the bobbin so my balanced tension is at 2. At 3 I was already pulling the bobbin thread up here and there. With the silk 100wt there is hardly any pull up of the bobbin thread because the bobbin thread and upper thread were more closely matched in weight.
In general, you will see that in the Zero-2 or 3 settings the top thread is pulled to the back of your work. The top tension is too loose. Most threads will show their ‘balanced’ tension between the 3 to 5 setting points. You will start to see the bobbin thread coming to the top between 6-8. The top tension is too tight.
Free Motion Tension:
When you are free motion stitching with the feed teeth disengaged you become part of the thread tension system. You may have to adjust your machine tension to compensate for the way you move the fabric. For example, I sew fast and move my fabric pretty fast too, so I usually set my upper tension to zero when I am free motion stitching with a rayon or metallic thread, and to 1 when I am using cotton or polyester threads. If I am relaxed and sewing slower, I may not change my upper tension at all.
I hope that helps solve all your tension issues! For more wild stitching adventures such as the moss stitch heart to the left, get my book; Threads: the Basics and Beyond written by Debbie Bates and myself.
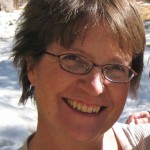
Liz Kettle is a mixed media and textile artist living in Colorado. She is co-author of 2 books, Fabric Embellishing: The Basics and Beyond and Threads: The Basics and Beyond. Liz loves teaching and sharing the joy of making stuff in her articles, classes and workshops. Visit her blog and website, www.TextileEvolution.com.